Safety & compliance
5 common dock safety mistakes – and how to avoid them
3 Apr 2024
Written by
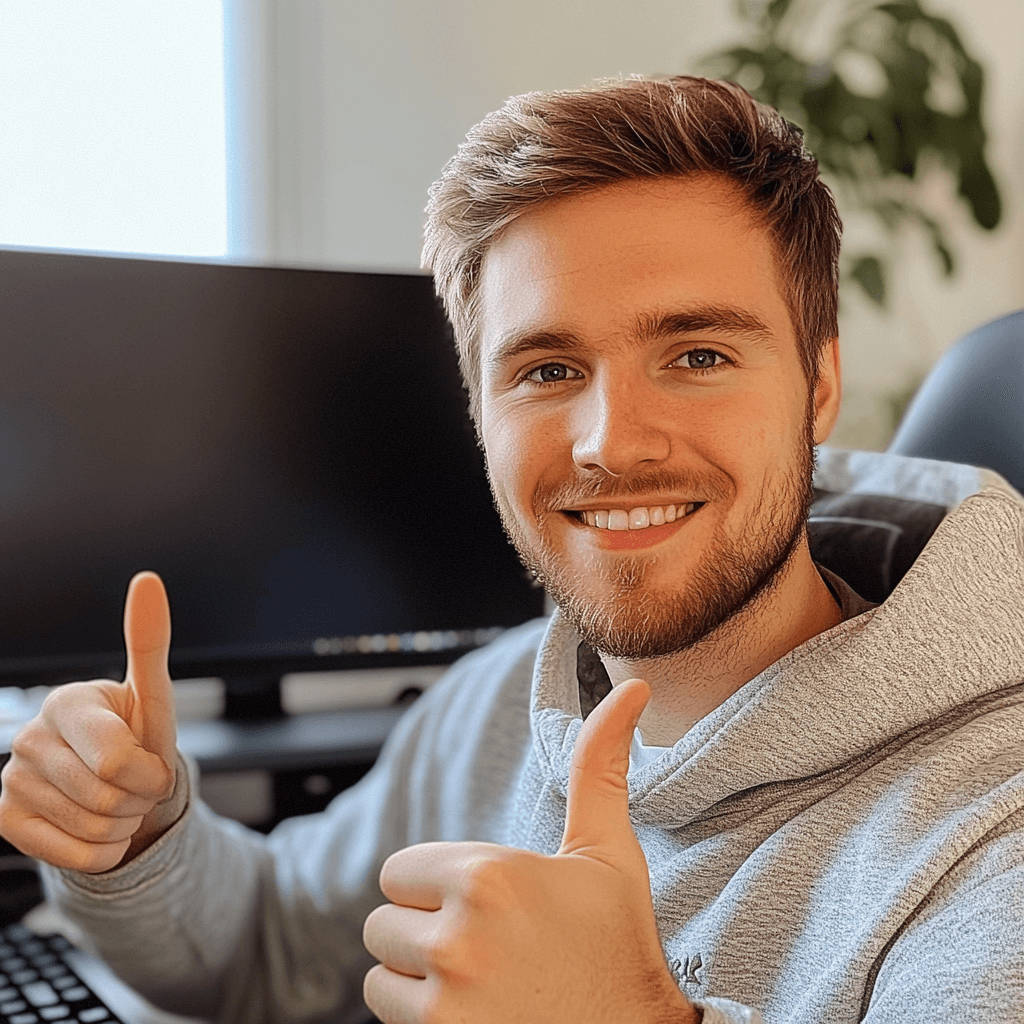
Mike Burton
Technical Advisor
Brings hands-on experience in installation, maintenance, and performance optimization of logistics systems. Focuses on maximizing reliability and safety of dock equipment in high-traffic environments.
Loading docks are among the busiest and most hazardous areas in any logistics facility. With constant movement of trucks, forklifts, dock equipment, and personnel, even a minor oversight can result in accidents, injuries, or costly damage. Despite growing awareness of occupational safety, many loading docks continue to struggle with common – and often preventable – safety mistakes.
In this article, we highlight five of the most frequent safety issues found in loading dock operations and explain how to avoid them using best practices, proper equipment, and a culture of safety.
1. Inadequate vehicle restraint procedures
The mistake:
Failing to secure the trailer properly during loading or unloading remains one of the top causes of dock-related accidents. If a truck moves or separates from the dock unexpectedly, workers inside the trailer can be seriously injured, and equipment can be damaged.
This often happens when:
Wheel chocks are not used or improperly placed
There is no powered vehicle restraint system in place
Drivers mistakenly pull away too early
The solution:
Invest in a reliable vehicle restraint system, such as:
Manual or automatic wheel-based restraints
Hook-based systems that latch onto the trailer’s ICC bar
Interlocked safety lights to prevent early pull-out
Additionally:
Use clear signage and driver communication protocols
Train staff on proper restraint use
Conduct regular inspections to ensure equipment functionality
2. Poor dock leveller maintenance
The mistake:
Dock levellers are critical for bridging the gap between the facility and the trailer. Yet many facilities neglect regular maintenance or delay repairs. Worn-out or damaged levellers can lead to:
Equipment malfunction or collapse
Slips, trips, or falls
Misalignment that damages goods or vehicles
The solution:
Establish a preventive maintenance schedule for all dock levellers. This should include:
Visual checks for cracks, rust, and hydraulic leaks
Testing safety features like lip extension and descent control
Lubricating moving parts regularly
Consider modernising older levellers with automatic deployment, push-button controls, or integrated safety interlocks that prevent premature use. Keeping levellers in top condition reduces downtime, liability, and long-term repair costs.
3. Inadequate lighting and visibility
The mistake:
Dock areas often suffer from poor visibility, especially in early mornings, late evenings, or during bad weather. Insufficient lighting can increase the risk of:
Forklift collisions
Misjudged vehicle docking
Trips over dock equipment or floor obstructions
Lighting issues are especially problematic in enclosed docks or those handling night-time deliveries.
The solution:
Upgrade to LED dock lighting systems that provide:
High-intensity, energy-efficient illumination
Adjustable arms to direct light inside trailers
Weather-resistant housings for outdoor use
Supplement this with:
Reflective signage and markings
Interior trailer lights
Exterior approach lights or dock traffic signals
Smart lighting improves both safety and operational efficiency, especially during fast-paced shifts.
4. Lack of safety barriers and dock edge protection
The mistake:
An open dock edge without physical barriers is a major fall hazard. Workers, forklifts, or pallet jacks can roll off the dock during loading, especially if the area is cluttered, wet, or poorly lit.
Falls from height remain one of the leading causes of workplace injuries in warehousing and logistics.
The solution:
Install dock safety barriers such as:
Manual or automatic safety gates
Dock edge chains or bollards
Protective railings or guardrails
Use wheel guides or alignment curbs on the approach lane to help drivers position vehicles correctly and reduce risk of misdocking.
Additionally, clearly mark all dock edges with paint or hazard tape and enforce safety rules about where workers can stand or operate machinery.
5. Poor communication between drivers and dock personnel
The mistake:
Miscommunication between truck drivers and warehouse staff can lead to serious accidents – like a driver pulling away while a forklift is still inside the trailer, or docking at the wrong bay.
This issue is especially common when:
The facility lacks a communication protocol
Language barriers exist
Safety lights or signage are missing or ignored
The solution:
Implement a standardized communication system, which may include:
Exterior dock traffic lights (red/green indicators)
Interior signal lights for forklift operators
Lockout/tagout procedures when the trailer is being loaded
Driver check-in protocols to confirm when loading is complete
Some advanced systems integrate proximity sensors and control panels that automatically block or permit movement based on loading status, enhancing overall dock safety.
Final thoughts: safety is a system, not an afterthought
While each of these safety mistakes can seem minor in isolation, they often compound under pressure. High-volume loading docks cannot afford to take shortcuts — especially when the risks involve human life, costly downtime, or damaged goods.
The good news is that most dock safety problems are preventable with the right equipment, clear procedures, and a culture of accountability.
Not sure where to start improving your dock safety?
Our team of experts is here to help. From product selection to system design, we’ll guide you toward solutions that keep your people, products, and operations protected. Let’s build a safer dock together.