Innovation & technology
Improving Efficiency with Proximity Docking Systems: A Technical Overview
24 Apr 2025
Written by
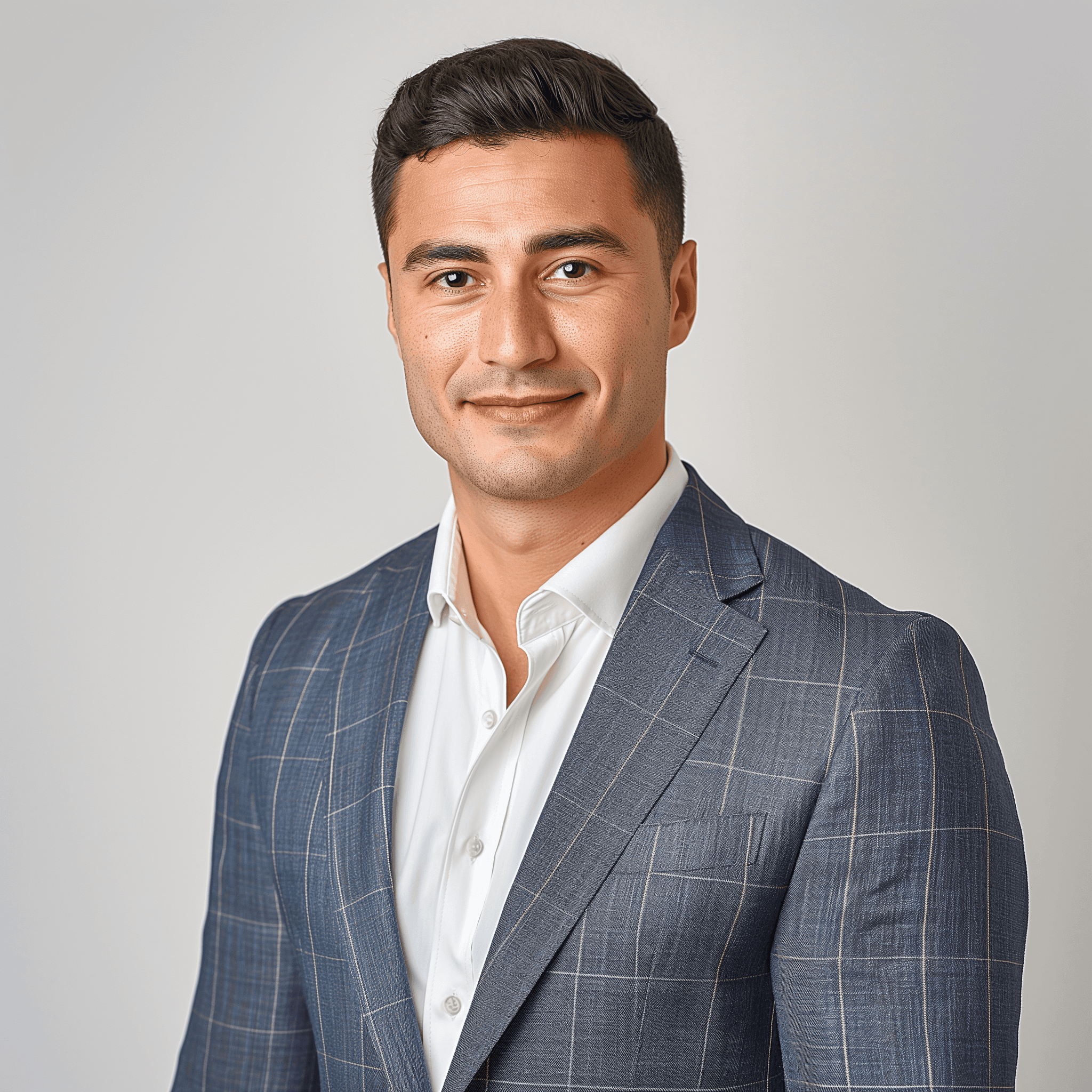
Alex Thompson
Sustainability & Compliance Expert
Expert in eco-efficient solutions and regulatory standards in the logistics sector. Provides guidance on sustainable production practices, including EPD-certified dock levellers and energy-efficient accessories.
Loading bay operations are a complex choreography of trucks, equipment, and people. Even a small delay or misalignment in the docking process can cause damage to vehicles, create safety risks, and reduce overall throughput. That’s why proximity docking systems have become an essential tool for logistics operations aiming to improve safety, precision, and efficiency at the dock.
In this in-depth article, we’ll explore what proximity docking systems are, how they work, the technical components involved, and how they contribute to operational excellence across various sectors.
1. What Are Proximity Docking Systems?
A proximity docking system is a sensor-based guidance system that helps truck drivers align their vehicles precisely with the loading dock. It typically uses sensors, lights, or even camera-based technologies to assist in the final stages of docking, minimizing the risk of collisions and improving positioning accuracy.
These systems are most commonly used in:
Busy distribution centers with frequent vehicle traffic
Docks with limited visibility or tight maneuvering space
Sites prioritizing safety and damage prevention
Proximity systems are not just “nice to have” — in high-throughput environments, they can significantly improve turnaround times and reduce long-term repair and liability costs.
2. Key Components of a Proximity Docking System
Understanding the anatomy of a proximity docking system is crucial to appreciating its value. Though designs vary by manufacturer, most systems include:
Ultrasonic or Infrared Sensors
Installed at strategic points on the dock or adjacent structures, these sensors detect the distance between the dock and the approaching vehicle.
LED Signal Lights or Displays
Clear visual indicators (usually red/yellow/green) guide the driver through the docking process — signaling when to slow down, stop, or adjust alignment.
Control Unit
A microprocessor-based control panel processes data from the sensors and drives the visual indicators. It may also log activity for later analysis.
Integration Ports
Many systems are designed to integrate with:
Dock levellers
Vehicle restraint systems
Warehouse management systems (WMS)
This ensures seamless operation and centralized control.
3. Technical Benefits of Proximity Docking Systems
Improved Docking Accuracy
By guiding drivers with real-time feedback, these systems minimize the chances of misalignment or off-center stops, which can delay loading and cause damage.
Faster Docking Times
Clear, intuitive signals reduce guesswork and speed up vehicle positioning, especially for less experienced drivers or foreign carriers unfamiliar with the facility.
Reduced Impact Damage
Accurate alignment lowers the risk of hitting dock shelters, bumpers, or the building structure itself — extending the life of these components.
Increased Safety
By removing the need for manual signals or spotters in the dock area, proximity systems reduce pedestrian exposure to moving vehicles, thus improving safety.
4. System Types and Technologies
Proximity docking systems are available in various configurations. Choosing the right one depends on your dock layout, traffic patterns, and operational goals.
Basic Sensor + Light Systems
These provide simple distance-based visual cues and are ideal for standard docks with minimal integration needs.
Example:
A truck approaches the dock — as it nears, a green light turns yellow, then red when it reaches optimal positioning.
Multi-Zone Systems
Offer advanced feedback based on multiple sensors that detect lateral alignment as well as rear distance.
Use case:
Docks handling varied vehicle types or large fleets with mixed trailers.
Camera-Based Docking Systems
More sophisticated systems using cameras and software to display docking angles and alignment feedback in real time (often integrated into the cab or a mobile device).
Use case:
High-security sites or temperature-controlled environments where precision is paramount.
5. Integration with Other Dock Equipment
The true power of proximity docking systems lies in integration. When synchronized with other equipment, you unlock process automation and smarter workflows.
With Vehicle Restraints
The system confirms accurate alignment before automatically engaging the truck restraint, ensuring a secure lock.
With Dock Levellers
The leveller activates only once the vehicle is confirmed to be correctly docked, preventing premature operation.
With Safety Lights and Doors
Signal lights inside the warehouse indicate dock status, coordinating with automatic doors or internal logistics systems.
6. Installation Considerations
Sensor Placement
Correct sensor location is essential for accurate readings. Sensors should be mounted at heights that accommodate your most common vehicle types.
Dock Condition and Lighting
Proximity sensors must not be obstructed or misaligned. Ensure proper maintenance of dock structures and lighting for optimal performance.
Power Supply and Wiring
Choose systems that align with your facility’s electrical infrastructure — wired or wireless options are available, each with pros and cons.
Environment
For outdoor docks exposed to weather, ensure the system is IP-rated for dust and moisture resistance.
7. Maintenance and Troubleshooting
Proximity systems are generally low-maintenance but should be inspected regularly to avoid false readings or communication errors.
Checklist:
Clean sensor lenses regularly
Check indicator lights for proper function
Test the system with various truck types
Ensure firmware or software is updated (if applicable)
Some advanced systems offer remote diagnostics and status reporting through a central control system or dashboard.
8. Return on Investment (ROI)
Though proximity docking systems involve upfront costs, the long-term ROI is compelling:
Benefit | Financial Impact |
---|---|
Less equipment damage | Reduced repair and replacement costs |
Faster turnaround | Improved throughput and scheduling accuracy |
Fewer accidents | Lower insurance and liability costs |
Better driver experience | Fewer complaints, higher retention |
Data tracking (on advanced models) | Smarter planning and operational insights |
ROI is especially strong when proximity systems are installed during new dock construction or renovation — minimizing retrofitting costs.
9. Future Trends: Smart Docks and Automation
The next generation of proximity docking will be even more connected and autonomous:
AI-powered image recognition to assess vehicle alignment
Integration with yard management software (YMS)
Real-time dock scheduling and driver assistance via mobile apps
Predictive maintenance using sensor diagnostics and analytics
Smart docks are no longer a futuristic vision — they’re quickly becoming standard in high-efficiency logistics environments.
Conclusion
Proximity docking systems are a simple yet transformative upgrade to any modern loading dock. By increasing accuracy, reducing damage, and streamlining workflows, they enable safer, smarter, and faster operations. Whether you're operating a small regional warehouse or a high-throughput distribution hub, these systems can bring measurable improvements from day one.
Need help choosing the right proximity docking system?
Our experts are here to assist you. If you're unsure which solution fits your loading dock, contact us — we’ll help you assess your site, define your needs, and choose the system that maximizes safety and efficiency.